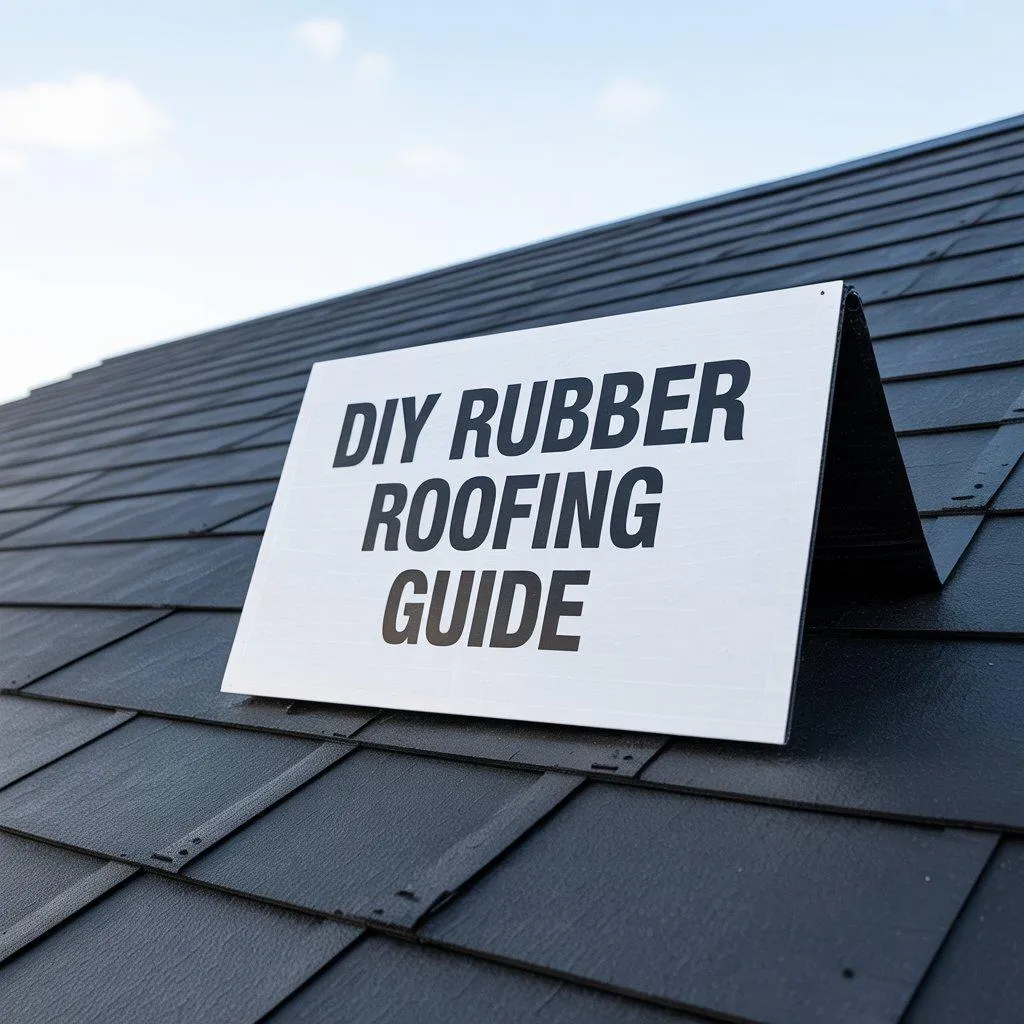
From My Tools to Your Roof: A Roofer’s Ultimate DIY Rubber Roofing Guide
I get it. You're looking at your flat or low-slope roof—maybe on a garage, a porch, or a shed—and you're thinking, "I can do that." As a roofer, I'm here to tell you that when it comes to EPDM rubber roofing, you're probably right. It's one of the most DIY-friendly systems out there.
But there's a difference between just getting it done and getting it done right. I've been called to fix plenty of DIY jobs that failed after the first big storm because of a simple missed step. This guide is my brain dump of everything I know. I’ll walk you through the prep, the process, and the pro-tips I’ve learned from years on the job to ensure your new roof is watertight for decades.
First Things First: Safety is Not Optional
Before we even talk about materials, let's talk about safety. Any roofing work has risks.
Ladder Safety: Always ensure your ladder is on stable, level ground. Use the 4-to-1 rule: for every four feet of height, the base should be one foot away from the wall.
Footwear: Wear soft-soled, high-grip boots. Hard-soled work boots can damage the roof deck and the new membrane.
Weather Awareness: Never work on a wet or frosty roof. A slight morning dew can make a roof deck dangerously slick.
1. Why I Recommend EPDM Rubber for DIY Projects
When homeowners ask me what to use for a flat roof, I often point them to EPDM (ethylene propylene diene monomer). Here's the no-nonsense breakdown:
It’s Tough as Nails: This stuff is built to last. It laughs at blistering sun, freezing temperatures, and hailstorms. A well-installed EPDM roof can easily last 30-40 years. It's the same material used on massive commercial buildings for a reason.
Budget-Friendly: Compared to other flat roofing systems, EPDM is very affordable. You're typically looking at $4–$10 per square foot for materials. Doing it yourself saves you thousands in labor.
Forgiving Installation: EPDM usually comes in one large sheet. For most residential projects, this means no seams. And where there are no seams, there are no leaks. This is the single biggest advantage for a DIYer.
2. Planning, Measuring, and What to Buy
Good prep is 90% of the job. Rushing this part is a rookie mistake.
Picking Your System
For almost all residential DIY jobs, I strongly recommend a fully-adhered system. It’s straightforward, creates a smooth, clean finish, and is incredibly resistant to leaks and wind uplift.
The Golden Rule: Check the Weather
Adhesives are picky. You need a dry spell with temperatures consistently above 40∘F (5∘C). The membrane, the deck, and the glue all need to be warm enough to bond correctly. Trust me, cold, damp weather is your enemy here.
Your Complete Tool & Materials List
Materials:
EPDM Membrane: Measure your roof length and width, then add at least 6 inches to every side for overhang and trim. Always round up.
Bonding Adhesive (Water-Based): For the main "field" of the roof.
Contact Adhesive (Solvent-Based): For the perimeter, walls, and vertical details. This stuff creates a much stronger, instant bond where it's needed most.
Seam Tape Primer & Seam Tape: Only if you have to join two pieces of membrane.
Peel-and-Stick Flashing: For pipes, vents, and corners. Don't skip this.
Lap Sealant Caulk: The final line of defense for all edges and seams.
Termination Bars & Drip Edge Trims: To professionally finish the edges.
Acetone or Splice Wash: For cleaning and priming areas before sealing.
Tools:
Push Broom & Dustpan
Leaf Blower (optional, but incredibly helpful)
Paint Rollers with medium-nap roller covers (one for each adhesive type)
Paint Tray
Utility Knife with plenty of extra blades
Tape Measure
Silicone Seam Roller (a small, hard roller for pressure)
Caulking Gun
Safety Glasses & Gloves
3. Prepping the Roof Deck: The Foundation of Your Roof
You cannot put a new roof on a bad foundation.
Inspect and Repair: Your roof deck, usually OSB or plywood, must be solid. Replace any soft, rotted, or delaminating boards.
Screws, Not Nails: Go over the entire surface and make sure it's fastened down securely with screws. If you see any nails or staples, pull them out and replace them with screws. A nail can back out over time and puncture your brand-new membrane from below.
Get it Surgically Clean: Sweep everything. Then sweep it again. Then use a leaf blower if you have one. A tiny pebble or screw left behind can work its way through the EPDM over the years. The surface should be clean enough to eat off of (but please don't).
4. Laying Out and Relaxing the Membrane
This is an easy step, but it's crucial for a wrinkle-free finish.
Unroll and Position: Unpack your EPDM sheet and roll it out over the roof. Make sure you have your planned overhang on all sides.
Let It Breathe: EPDM is packed tightly for shipping and will have creases and wrinkles. Leave it to "relax" for at least 30-60 minutes. This allows it to acclimate to the temperature and lay flat, making it much easier to glue down smoothly.
5. Applying the Adhesive: Where the Magic Happens
This is a two-part process. Don't mix up your glues.
A. The Field (Water-Based Bonding Adhesive)
Fold the relaxed membrane back over itself to expose half of the roof deck.
Pour the water-based adhesive onto the exposed deck. Use your roller to spread it evenly, just like you're painting a floor. You're looking for a consistent, light-pink or white coat (depending on the brand).
Let it get tacky. Don't roll the membrane back immediately. Wait until the adhesive is just tacky to the touch.
Carefully and slowly roll the membrane back over the glued deck.
Grab your clean push broom and, starting from the center, broom the membrane towards the edges. This pushes out all the air bubbles. You can't overdo this step.
Repeat the entire process for the other half of the roof.
B. The Edges (Solvent-Based Contact Adhesive)
The perimeter (the outer 6-12 inches) and any vertical walls need a stronger bond. This is where contact adhesive comes in.
Fold back the edges of the now-adhered membrane.
Apply a thin, even coat of contact adhesive to both the roof deck perimeter and the underside of the EPDM membrane.
This is critical: Wait for it to become touch-dry. When you gently touch it with a knuckle, it should feel tacky but not string off or transfer to your skin. If you bond it while wet, you'll get a weak seal full of bubbles.
Carefully press the membrane edge into place. This bond is instant and permanent, so you only get one shot to get it right.
6. The Details That Prevent Leaks: Seams, Corners & Flashing
This is where a pro earns their money and where a DIY job often fails. Take your time here.
Seams: If you must have a seam, overlap the sheets by at least 3 inches. Clean both surfaces with primer, apply the seam tape, and then use your silicone roller to apply firm pressure along the entire length. Finish the exposed edge with a thick bead of lap sealant.
Inside & Outside Corners: Don't try to stretch the membrane around a sharp corner. It won't work. Form a "pig's ear" fold by pinching the excess material together, then fold it flat against the deck. Use peel-and-stick corner flashing over the top for a bulletproof seal.
Pipes & Vents: Use pre-made pipe boots or peel-and-stick flashing. Cut a hole slightly smaller than the pipe, stretch the membrane over it for a tight fit, and then flash it properly. Seal the top edge with lap caulk.
7. Finishing the Edges for a Professional Look
Trim the Excess: Use your utility knife to trim the overhanging membrane flush with the edge of the roof.
Install Edge Trims: Secure your metal drip edge and termination bars. These give the roof a clean look and direct water away from the structure.
Final Seal: Run a generous bead of lap sealant along the top of all edge trims and anywhere the EPDM meets another surface. Tool it with your finger for a clean, watertight finish.
8. Final Inspection and Water Test
Walk the roof and look for any "spongy" spots that might be air pockets.
Use your seam roller one last time on all flashed areas to ensure a tight bond.
If you're confident in your seals, do a water test. Gently flood the roof with a garden hose and let the water sit for an hour. Check for any pooling and ensure your drains or drip edges are working correctly.
9. Common Mistakes I've Seen (And How to Fix Them)
Even with careful work, issues can pop up. Here are the most common problems I get called to fix and how you can handle them yourself without needing a special table format in your blog post.
Problem: Bubbles and Wrinkles Appear in the Roof
Likely Cause: This usually means trapped air wasn't fully pushed out with the broom, or the adhesive was applied unevenly and dried too quickly in some spots before the membrane made contact.
The Roofer's Fix: For small bubbles, you can often still push them toward the nearest unglued edge with a steady hand and a roller. For a large, stubborn bubble, you’ll have to perform minor surgery: carefully make a small slice in it with your utility knife, press the air out, inject a small amount of adhesive with a caulk gun, press it flat, and then clean and patch the slice using seam tape and lap sealant.
Problem: The Membrane Is Shrinking and Pulling Away from the Edges
Likely Cause: This is a classic sign of a bad perimeter bond. It almost always happens because the solvent-based contact adhesive was not allowed to dry to a tacky state before the membrane was pressed into it.
The Roofer's Fix: Unfortunately, this is a serious issue that needs a proper fix. You will need to cut away the failed section of the membrane. Re-apply contact adhesive to the deck and a new piece of EPDM, letting it cure properly this time. Then, install the patch piece and create a new, waterproof seam to join it to the main roof sheet.
Problem: A Seam or Flashed Area Is Leaking
Likely Cause: The leak is almost certainly due to contamination (dirt, dust, or moisture) on the membrane when the seam was made, or not enough firm pressure was applied with the silicone roller to create a permanent bond.
The Roofer's Fix: You cannot cut corners here. Scrape away all the old lap sealant. Using an approved EPDM cleaner or acetone, you must get the area surgically clean. Once it's dry, re-prime the surfaces, apply new seam tape or flashing with firm roller pressure, and finish the edge with a fresh, generous bead of lap sealant.
When to DIY vs. When to Call a Pro
A simple, square garage roof is a fantastic DIY project that can save you a ton of money. But if your roof is large, has multiple levels, lots of pipes, vents, or an HVAC unit on it, the risk of a leak goes up exponentially.
This guide gives you the blueprint for a professional-grade installation. But if you're standing on the edge and feeling overwhelmed, that's what we're here for. The Artigues Roofing team has tackled countless rubber roofs, and we can guarantee a flawless finish.
Ready to start your project or want a second opinion?
Explore our work: Past Works
Get a professional quote: Contact Us for a free, no-obligation inspection